「100分の1ミリ、1000分の1ミリを自在に
操ってこそ職人の技です」
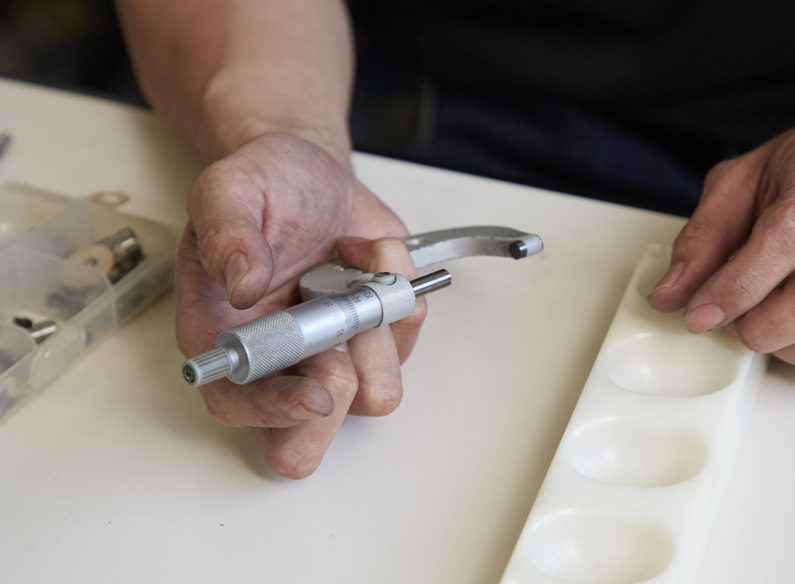
特に指定が無ければ、一般的には図面のサイズに対して、誤差がコンマ1ミリ、つまり10分の1ミリ程度に抑えてあれば切削加工としては問題ないのですが、ついつい100分の1ミリ、1000分の1ミリまで追ってしまうんです。
本来、100分の1ミリ、1000分の1ミリの領域は研磨加工の仕事で、私たち切削の仕事ではないので自分でも「ここまでしなくても」と思うのですが、実際に作業をしているとどうしても気になってしまいます。
私が作るものは、ほとんどが一点物の試作品です。多くの場合、全体の中の一部品で、納品した後に納品先で他の部品と合わせて組み上げることになるのですが、その時のことを考えて、ピッタリ組み合わされたら気持ちいいだろうな、なんて考えるんです。
ただ、実際は1000分の1ミリレベルまで追い詰めると逆に組み立てづらいこともあるんですよね。
例えば、筒の中に棒状の部品を入れるとすると、1000分の1ミリまで追い込んだ場合、完璧に真っ直ぐに入れなければ斜めになって部品同士が擦れ合って入らなくなります。最低でも1000分の5ミリ、物によっては最低でも100分の1ミリくらいは余裕を見ておかないと組立ができません。
ただ無闇に精度を追うのではなく、その辺りを上手に見極めるのが職人の技量になるのではないかと思います。
また、樹脂などの軟らかい材料はもちろんですが、金属材でも材質によって温度による変化の度合いが異なります。
現場で正確に切削したつもりでも、納品先で微妙に温度変化が起きてサイズが変わることもあります。そうしたことを考慮しながら精度を出していくのも私たちの大切な仕事です。
優れた職人の技術というのは、1000分の1ミリを出せる指先の技術を、状況に応じて自在に使いこなせることだと思います。
「優れたコンピュータで制御される今でも、
重要なのは人間の想像力です」
そうした職人ならではの能力が求められるのは、コンピュータで数値制御された最新の機械になっても変わらないと思います。
現在、複雑な形状の切削には、いくつもの工具を自動で交換するコンピュータ制御の切削機械、マシニングセンタを使っています。
単純な円形状の切削であれば使い慣れたベンチレース(卓上旋盤)などの方が早いのですが、複雑な突起部を持った形状となるとマシニングセンタが必要です。
マシニングセンタは一度セットしてしまえば自動でやってくれますから、製作工程は圧倒的に早くなります。
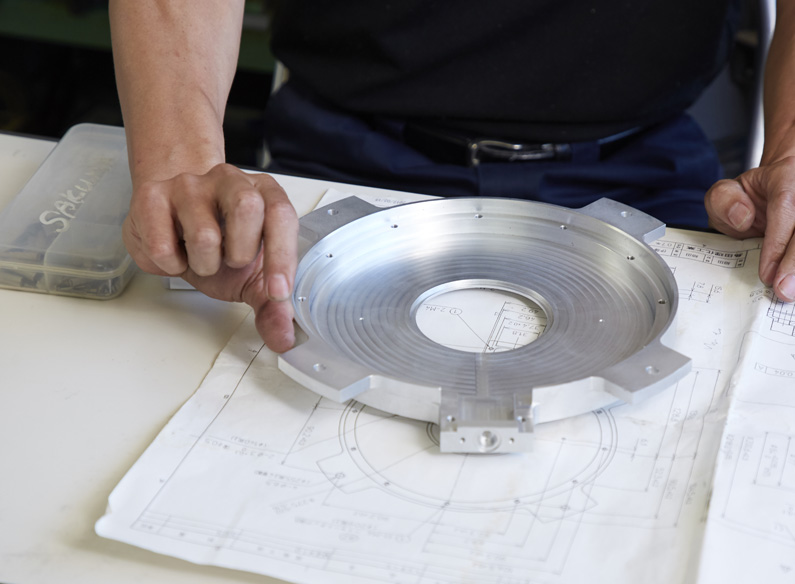
ただ、重要なのはどういう順番で切削を進めるかということです。これは人間が決めなければなりません。
例えば、ひとつの材料を削っていく場合、削ることで材料自体の強度が変わってきます。それを計算して工程を考えていかないと精度が出せなくなってしまいます。
私の場合、材料を直接マシニングセンタにセット(挟んで固定)するのではなく、材料をセットする治具を自作して、その治具をマシニングセンタに固定します。そうすることで、材料に余計な負荷がかからないようにするのですが、その治具を作る時に、まず頭の中で工程をシミュレーションして、どこにどのような負荷がかかるかを考えます。
その想像力が、より高精度で、より効率的な切削を可能にします。
「マシン油からKURE 5-56 へ。
父の時代から私の時代へのひとつの変化」
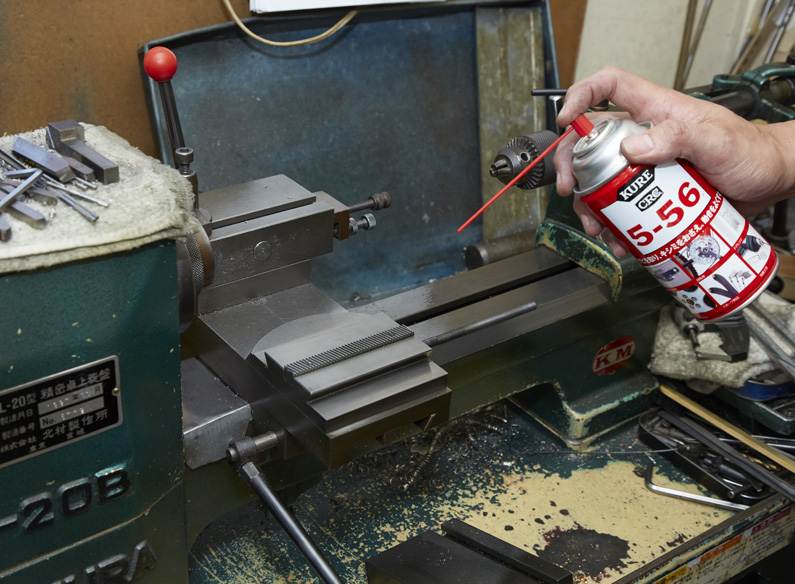
子供の頃からベンチレース(卓上旋盤)が身近にあり、遊び半分で使ってみたりもしていましたが、とにかく機械全体が油まみれで、どこを触ってもベタベタしていました。
当時はそれが当たり前で、削り粉で黒くなった父の手も、職人の手という感じがして誇らしかったものです。
ただ、実際に仕事として自分で毎日使うようになると、ベタベタした油にこびり付いた金属の切粉の掃除が大変でした。それに、機械用に使うマシン油というのが業務用の一斗缶(18リットル)でしか買えなかったので、ウチの工場で使うレベルだと、それこそ何年分という感じで多すぎてしまいます。
そこで、ふと思って家に昔からあったKURE 5-56 を使ってみたら、これがとっても良かったんです。
マシン油のように粘りがないので汚れがキレイに吹き落とせますし、台座や刃の細かなところにも吹き付けやすい、隅の方までシッカリ染み込んでいくのも使いやすいです。 主にサビ止めと潤滑のために使っていますが、4〜5日に一度の割合で使えば十分なので使い勝手もいいです。
それから、マシン油からKURE 5-56 に替えてから手が汚れなくなったんです。昔の職人気質の手も好きですが、普段の生活を考えると、やっぱりキレイな方がいいですね。
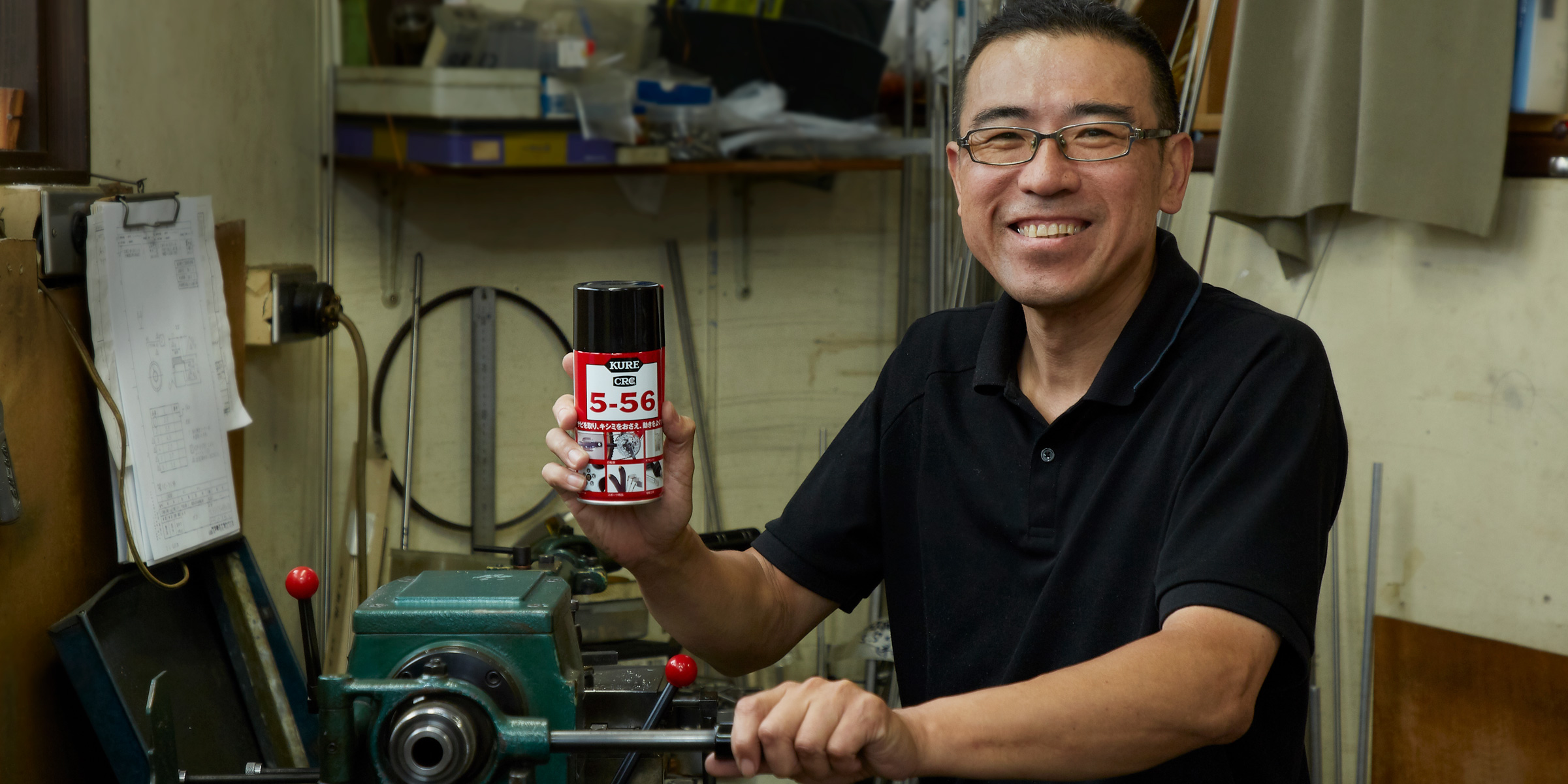
「日本人だからこそできる
職人技術の真髄を伝えていきたいです」
私が関わる仕事は多岐にわたります。一般的な工作機器から精密機械、CDプレーヤーのパーツ、宇宙ロケットの部品など。中には医療用透析器のポンプ部など、非常に複雑で繊細な形状の物も少なくありません。
指先の感覚で操作するベンチレースにしろ、コンピュータ制御されたマシニングセンタにしろ、より良くしたい、わずかな狂いも見逃したくないという日本人ならではの細やかな気持ちがなければ、よい製品は作れないと思います。
最近よく「職人の技術を再現」という言葉を耳にしますが、それは数値的な精度の話であって、日本の職人ならではの細やかな気配りが再現されているわけではありません。
最先端の機械が世界中で使われるようになったからといって、どこの国でも本当に優れた製品が作れるかというと、そうではないような気がします。日本の職人が積み重ねてきた技術だけでなく、経験、そして想像力が無ければ、世界に誇る「日本の技術」に世界が追いつくのは、まだまだ先のことではないでしょうか。
今の技術だけでなく、父や先輩の技術者から受け継いできた職人技術やその真髄を、次の世代に伝えていきたいです。
Profile
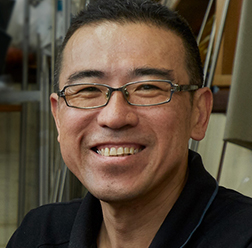
佐久間 正巳(さくま まさみ)
株式会社 佐久間製作所 代表取締役
1965年 東京都大田区生まれ
1984年 大田区羽田の専門学校(旧・職業訓練校の機械科)入学
1985年 卒業後、実家とは異なる技術を求めて町工場に就職
1987年 初代「大田の工匠」の一人である父・幹夫氏が1962年に創業した佐久間製作所を受け継ぐ
1990年 警察警棒が従来の木製から伸縮式の金属製となるにあたって開発に参加
2013年 ドラマの制作に参加、旋盤指導を行う
2014年 「大田の工匠100」に選出